Micro Molding and Micro Optics
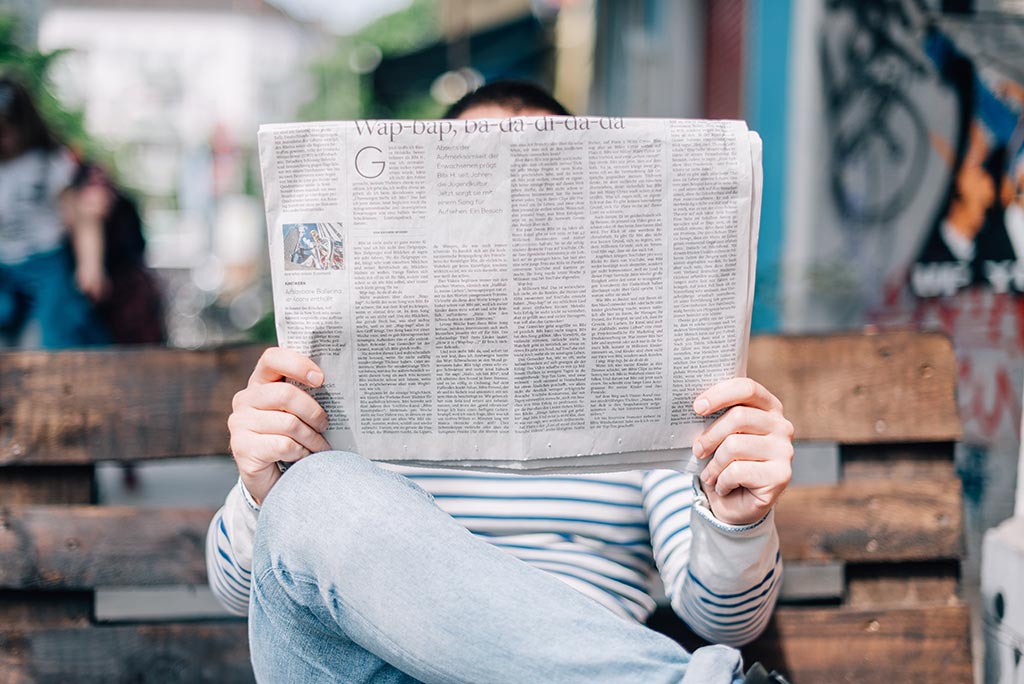
By Aaron Johnson, VP of Marketing and Customer Strategy, Accumold
As is often the case when attempting to define anything in the area of precision, micro, and nano manufacturing, trying to set some sort of size parameters around what are considered “micro”-optics is difficult. In general terms, however, micro-optics are typically tiny lenses, beam-splitters, prisms, light-pipes, and other optical components in the range of 20 microns to 1 mm in size, or larger optical components with micron features.
Wherever light is involved, micro-optics offer a possibility for OEMs to further miniaturize a product, increase its functionality, and/or simultaneously reduce manufacturing costs. Micro-optics are used today in an array of medical applications such as endoscopes and ophthalmic systems, in industrial inspection equipment, in laser-based devices and fiber communication networks, in modern smart phones, and any devices using digital camera technology, ambient light or proximity sensors.

Typically, OEMs engage specialist micro molders such as Accumold to assist in the manufacture of customized products. Key in the selection process is a company with experience in the field, and an understanding of — and ability to manufacture to — the exacting tolerances demanded. In addition to quality, however, another key driver is adherence to often short time-to-market requirements.
Micro-optic components are characterized not just by how small they are, but also by their flatness, with the surface relief feature depth of diffractive optical elements (DOEs) being in the range of a few hundred nanometers to a few micrometers. Even refractive micro lens arrays typically have relief depths of less than 100 microns. Such flatness characteristics have opened up the use of production technologies such as injection molding which offer significant cost advantages as component volume increases. Use of injection molding for micro-optic manufacture, however, requires the optimization of design, mastering, tooling, and production steps, meaning a close interaction between supplier and product developer is vital.
PLASTIC vs GLASS
Superimposed upon the recent history of micro-optics is the increased popularity of plastic as a manufacturing material rather than glass. As the market expands, and the demand for modern optical applications increases, polymer-based injection molded optics are now found in a broad range of products.
Today micro-optic fabrication is split in two: the supply of key components in low volume for laser, telecom, medical and metrology applications; and the supply of high volume and low-cost micro-optics for the consumer market. Key drivers behind both areas has been the increasing sophistication of micro-injection molding technologies, as well as dramatic developments in materials, which means that today, complex, miniature, and previously fragile micro-optics are now robust, and can withstand even the harsh environmental requirements of the consumer electronic industry including infrared (IR) reflow and thermal shock. Working in plastic also introduces enormous design freedom.
Injection molding is the only viable manufacturing technology to use when low-cost, high-volume production runs are required. A single tool is capable of mass-producing plastic micro-optic parts (including necessary surface finish), and if process controls are rigorous enough, 100% accurate replication is possible run after run. This is not the case when manufacturing in glass.
In addition, mounting and mechanical features such as spacers and flanges can be integrated into plastic optical components, thereby removing the need for additional components and assembly considerations. Unique cosmetic, functional filter, and other properties can also be added to enhance or improve the properties of the raw molding polymer, which again cannot be done with glass.
PARTNER CHOICE
The overall micro-optic manufacturing sector is characterized by high costs and high risks, with few qualified and reliable manufacturers available that can manufacture to the level of accuracy required, in the timeframe required, and at a sensible and competitive cost. Like all niche micro manufacturing sectors, it is especially vital in the area of micro-optics that qualified micro-optic suppliers such as Accumold are engaged as early in the design process as possible and are treated as a product development and manufacturing partner rather than a job-shop. It is only by doing this and being able to superimpose specific micro manufacturing and micro-optic expertise on a particular project that an efficient and cost-effective solution can be realized.
Of vital concern when choosing a qualified partner is an understanding of the necessity for qualified and expert testing and quality assurance processes that are unique to micro-optic fabrication. There are numerous challenges when attempting to manufacture micro-optic devices and components which demands that OEMs choose to partner with companies such as Accumold, with a proven track record and years of experience manufacturing to the tightest tolerances and the most exacting standards achievable.
Of the manufacturing processes used for production of plastic micro-optics, injection molding is the most established, although it is also possible to use UV embossing and hot embossing. All require either a mold or an embossing die to shape the optical component. Inserts for molds or embossing tools need to be extremely precise (sometimes to less than 90 nanometers), and with extremely low surface roughness characteristics. Such tolerances can typically be achieved through the use of single-point diamond turning technologies that can be used to cut complex optical surfaces with sub-micron accuracy.
Very often, it is possible to use precision injection molding machines using traditional multi-cavity tooling for mass production of many micro-optic components, but for ultra-precise and very small components, it is usually necessary to use specialized micro molding machines which typically exhibit a higher inject speed, precise shot control, and ultra-fine resolution for molding small sized parts.

In principle, it is fair to say that micro-optic components (that is to say micro scale components not larger parts with micro features) are just scaled down macro-optic parts. It is this scaling down, however, that requires the understanding and skill of a specialized micro manufacturing agency. Mechanical tolerances that companies may find very easy to achieve on larger optical components may not suffice on micro-optics, where any variation corresponds to a much greater percentage of error and could massively impact the performance of a lens or other micro-optic components. Overcoming such problems requires special focus on tool construction, for example, and the achievement — typically — of sub-5 micron tolerances.
Accumold routinely assists in the design, tooling, and manufacture of micro-optic devices such as 250-micron fiber optic lenses, parallel array products, demux devices, and diffractive lenses. The company also has experience of molding attenuated resins and adding IR, anti-reflective (AR), and reflective coatings onto plastics. The demands associated with running micro-sized optical couplers, integrating lenses into housings, replicating lens profiles within a quarter wave, and lens surface finishes within 50 angstroms requires that Accumold has a dedicated tooling expert on staff to advise on and optimize design for manufacturability and tooling for any OEM light transmission requirements.
But tooling challenges are only one consideration. Also of key importance is molding process parameter control, metrology equipment capabilities, and post molding handling and assembly.
Precise control of the shot size or volume of resin injected into the mold on each cycle is vital for the maintenance of accuracy and repeatability of micro-optics shot to shot and run to run. Once molded, however, it is important to use a fully automated and hands-free assembly process, overcoming the basic logistical issues surrounding the removal of such tiny and delicate components while also ensuring that orientation is maintained and parts are not contaminated by touching.
Micro-sized features on larger optical parts are usually found on lenses that incorporate small optical features, such as refractive elements with individual apertures from a few microns to a few millimeters, or diffractive features that consist of patterns produced on a micron scale. Here, the accuracy of the optical surfaces are the most critical detail, and the fabrication process for the optical mold inserts presents the largest challenge. These features are typically machined directly onto the base curve of the tool inset using ultra-precise technologies that allow for the manufacturing of complex, non-rotationally symmetric, optical structures. Alternatively they can be applied using photo-etching technologies.
The extremely tight tolerances that are characteristic of micro-optic applications — coupled with the demands for expertise in tool construction and material selection — require that OEMs undertaking a micro-optic project engage with a partner such as Accumold in development to ensure accurate, timely, and cost-effective manufacturing solutions.

Aaron Johnson is the VP of Marketing and Customer Strategy at Accumold. The company has grown to a 130,000 square foot fortified facility designed for assurance of supply, employs over 350 staff, and is a net exporter shipping all over the world every day from its Ankeny, IA, USA facility which runs 24 hours a day, 7 days a week.