China’s government eyes complete scrap import ban
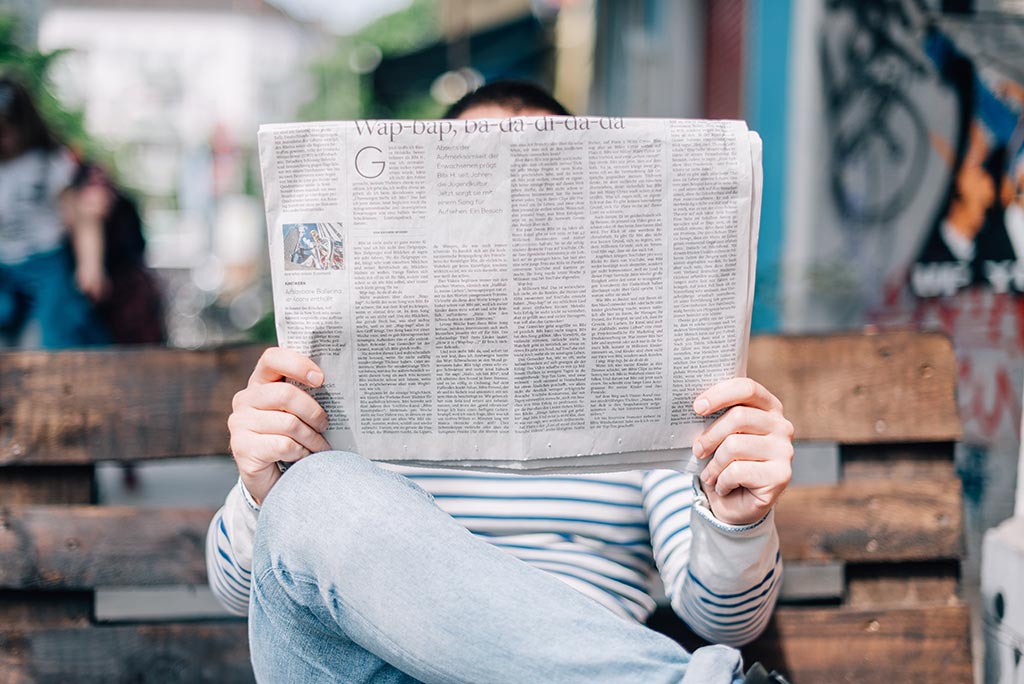
Reports indicate nation’s State Council may favor total scrap import ban by 2021.
Who’s effected?
Recycling Equipment Manufacturers and Recycling Companies

For a closer look, let’s review the equipment that will be affected:
Balers are used to push materials together and compact them so that they can be formed into bales, or block-like shapes, that are easy to stack and transport. In recycling facilities, recovered materials are put into a baling machine after being sorted. This way, entire bales of plastic or metal can be shipped to manufacturers to be melted down and reused for brand new products.
For manufacturers in industries that use recycled materials to create new products, compact bales are very convenient. They can be stored for processing at a later time, and easily moved around a factory using a forklift. Most factories are at maximum efficiency during high production, so it is optimal to have large amounts of material that can be melted all at once.
In many recycling and recovery plants, scrap and waste materials are often stored in large piles to be processed at a later time. For these kinds of facilities, the use of a grappler is often the most effective method for introducing these piled materials into the recycling and recovery process. Grapplers can pick up large quantities of scrap material from these storage piles and place or feed the material into processing equipment, like material separators, shredders, and balers.
A scrap handling magnet is very similar to a grappler but uses electromagnetic forces to attract and hold objects instead of mechanical force. Scrap handling magnets consist of an electromagnet connected to a chain on the end of a hydraulic arm that can raise and lower it. Scrap handling magnets come in a variety of sizes, but they are usually round and the top portion is encased in a strong metal body to protect the magnet and hold it firmly in place during use. The magnets used to lift scrap metal can be powerful enough to pick up thousands of pounds at a time, and they are frequently used in facilities that specialize in metal recovery.

Industrial metal shears are used to cut large pieces of metal, particularly sheet metal. The shearing machine cuts the metal into thin strips as it is fed into the machine, turning it into dozens of smaller pieces that can easily be transported, melted down, and used again for another product.
designed to take place on a perfect 90 degree angle since it actually requires less force to cut diagonally through the material. For this reason, many metal shears have angled blades.

Material separation is an important first step in the recycling process. Recovering products from the waste stream and making sure that they end up in the right category to be recycled is difficult but essential to efficient recycling practices. Recycling plants are always trying to raise their recovery rate to keep as much material as possible out of landfills and lower energy consumption by making new products out of these used materials. The right separation equipment properly tuned for a specific application will always play a serious role in creating a greater rate of recovery. Workers can separate some materials manually, but separation is always more effective with the aid of a machine, particularly when dealing with high volumes of material.
As technology improves and more and more recovery centers do everything they can to raise their recovery rate, more materials are able to be eliminated from the waste stream and repurposed for new uses. The result is a reduced impact on landfills and a healthier approach to environmental care. Material separation equipment plays a key role in helping to maximize the efficiency and effectiveness of this process.
Magnetic separators assist in separating ferrous materials from non-ferrous materials. This is accomplished by exposing the unsorted material to a powerful magnet that is mounted over a conveyor belt or in a chamber. The magnetic force pulls out the ferrous metals, and leaves the rest. Magnetic separating equipment is very convenient in metal recycling facilities because it keeps material moving in scrap yards and other high volume facilities.

Shredding equipment is critical to the recycling process because it breaks down tough materials into smaller, more manageable parts before they are baled or made into a more convenient form for reuse. Different types of shredders are used for almost every kind of material that you can imagine; from rubber to plastic to metal and beyond. Because they are needed for so many different applications, shredders are manufactured in a wide variety of sizes and styles. Document destruction, for example, is much less heavy duty than metal shredding, so manufacturers create machines that meet the needs of each industry. One application that has seen a significant increase in shredding over the years is electronic scrap processing. Because there are now so many old electronic devices on the market, it is necessary to find ways to break them down and reuse their components. In certain cases, Pulverizers are used for many size reduction requirements.

A vibratory feeder, also known as a vibratory conveyor, is a type of equipment that uses vibrations to transport bulk material through stages of a particular process, like packaging, recycling, or finishing. Vibratory conveying differs from standard belt, screw, and pneumatic conveying in that it can handle sticky or delicate materials without damaging them or causing them to liquefy. Vibratory feeders are ideal machines to use for material handling as they are low-maintenance, and the only moving part it contains is a vibrating drive located underneath the feeder pan and out of the way of any materials. The other parts of a vibratory feeder are inexpensive and easy to replace. Vibratory feeders can be powered either electromagnetically or electromechanically, the latter of which is driven by a motor supported by eccentric weights or an eccentric crank.
There are several main types of vibratory feeders. The first, vibratory bowl feeders, are also referred to as centrifugal feeders or vibratory bowls. These feeders are used by parts manufacturers to align finished or semi-finished parts to prepare them for packaging. The second, vibratory conveyors, covers a broader range of troughs, trommel screens, and vibrating screens that are made for the purpose of conveying and sorting bulk materials. The third, rotary feeders, are also referred to as rotary valves or rotary airlocks. They transfer airtight bulk material to vibratory or screw conveyors. The fourth and final category is linear feeders, or inline feeders, which are commonly used to transport parts from bowl feeders in a vibratory linear motion for short or relatively long distances.
Many industries—such as food processing, agricultural, and pharmaceutical—use vibratory conveyors, screens, and trommels for bulk and powder material handling Vibratory conveyors are used frequently in recycling industries to sort and convey numerous materials such as metals, crushed cement, wood, and plastic. Mining, pulp, sand and gravel, and fertilizer companies use vibrating screens and trommel screens to sort, sift, and convey their materials. A grizzly screen is a powerful type of vibrating screen which is most frequently used in the mining industry. Vibratory conveyor systems usually work together with rotary airlock feeders when they must convey powder bulk solids. In the processes of reclamation or collecting dust, rotary feeders and dust collecting systems are used together.
Conclusion The action by China will affect many equipment manufacturers and their customers and the long range effect will be damaging to our economy. A swift resolution to our trade imbalance is necessary for our economy to grow.