3 Keys to Keep Electronic Enclosures Waterproof
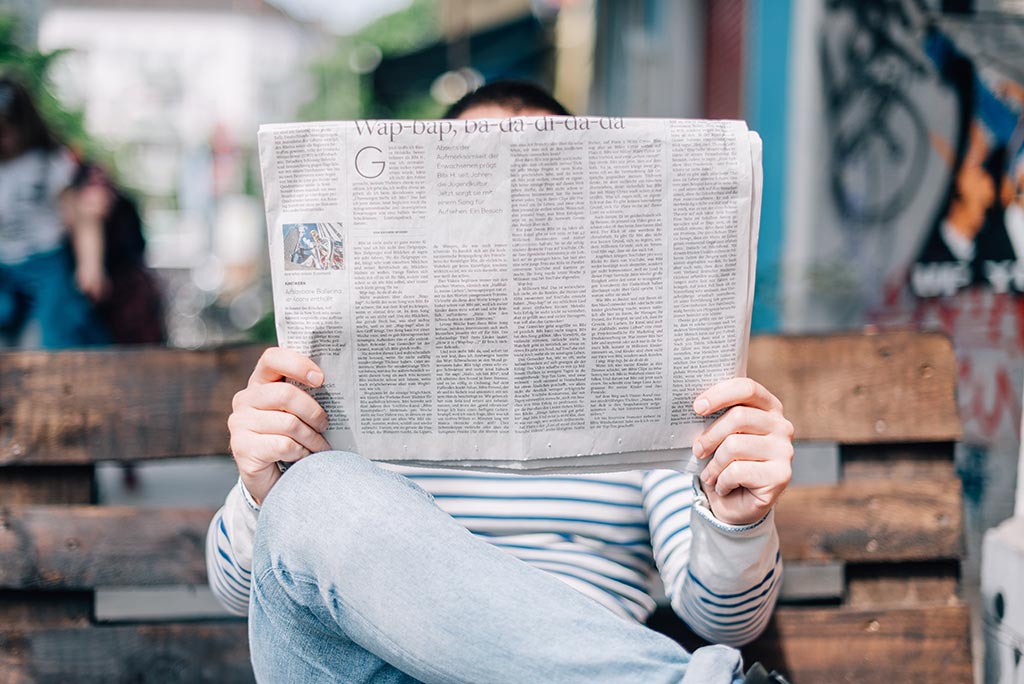
Since Sony popularized water-resistant smartphones with the Experia Z in 2013, demand for waterproof electronics has soared. Waterproofing is now standard for new smartphones, and demand for rugged phones that include water-resistant features is increasing at a compound annual growth rate (CAGR) of 18.9 percent. Demand for waterproof speakers is likewise growing at a CAGR of 7.0 percent, while the market for waterproof connectors is also set to grow exponentially.
Meeting the need for water-resistant electronics depends on the ability to produce waterproof enclosures. Here are some tips for making sure that electronic devices stay secure when submerged in water.
Use Simple Sealing Shapes
Waterproofing protection is measured by the International Electrotechnical Commission’s International Protection Marking or Ingress Protection Marking (IP Code) system, which uses a scale of 0 to 8 that ranges from protection against vertically falling drops of water to protection against sustained immersion under pressure. Experience has shown that simple circular shapes such as o-rings provide optimal sealing for electronic closures by exerting uniform, continuous force.
Conversely, complex designs requiring seals between multiple parts prove more difficult to waterproof. Aim for designs that minimize sealing surfaces between three or more parts. If you need a more complex seal, consider a tortuous design with repeated twists. Designs using compressive methods such as bulkhead fitting are more reliable than ones with other methods such as wedge fitting.
Choose Stable Materials
Material selection plays an important role in optimizing waterproofing designs. Materials that are prone to change size or shape or stiffness under live conditions may not be suitable for applications that demand waterproofing. Suitable materials should have properties that tend to maintain stability when used with the intended application. For instance, Viton and silicone o-rings have high temperature and chemical resistance, making them popular for electronics applications, and they also have excellent water resistance. A knowledgeable supplier can help you select the right material for your application.
Alternatively, if your design doesn’t lend itself to an o-ring or gasket shape, elastomers such as Viton can be used as sealing enclosures through overmolding by directly affixing them to one half of your enclosure. Other alternatives include liquid adhesives and ultrasonic welding.
Provide Proper Support
Solid support is critical for ensuring waterproof seals. If a gasket or o-ring moves out of its proper pinch zone, a seal can leak or fail entirely, especially under pressurized conditions.
To prevent this, non-circular standalone gaskets should receive firm support from all sides. Support should be sufficient to keep the gasket in place under whatever amount of pressure it will be subjected to under live application conditions. For high-pressure applications such as hydraulic use, circular o-rings are generally more suitable than gaskets made of substances such as cork, paper or standard rubber.
Waterproofing electronic enclosures effectively requires paying special attention to key best practices. Simple circular shapes supply superior seals, making o-rings especially suitable. The fewer sealing surfaces between multiple parts the better. When complex shapes are needed, tortuous twists can help keep designs manageable. Materials selected for stability will serve better than materials that tend to shrink or stretch. Options such as overmolding, liquid adhesion and ultrasonic welding can be useful alternatives for certain applications. Firm support will help keep gaskets in their pinch zone to prevent leaks. Following these guidelines will help keep your electronics enclosure waterproof.