Robot Gripper – Selecting the Right Robot Gripper for Your Applications
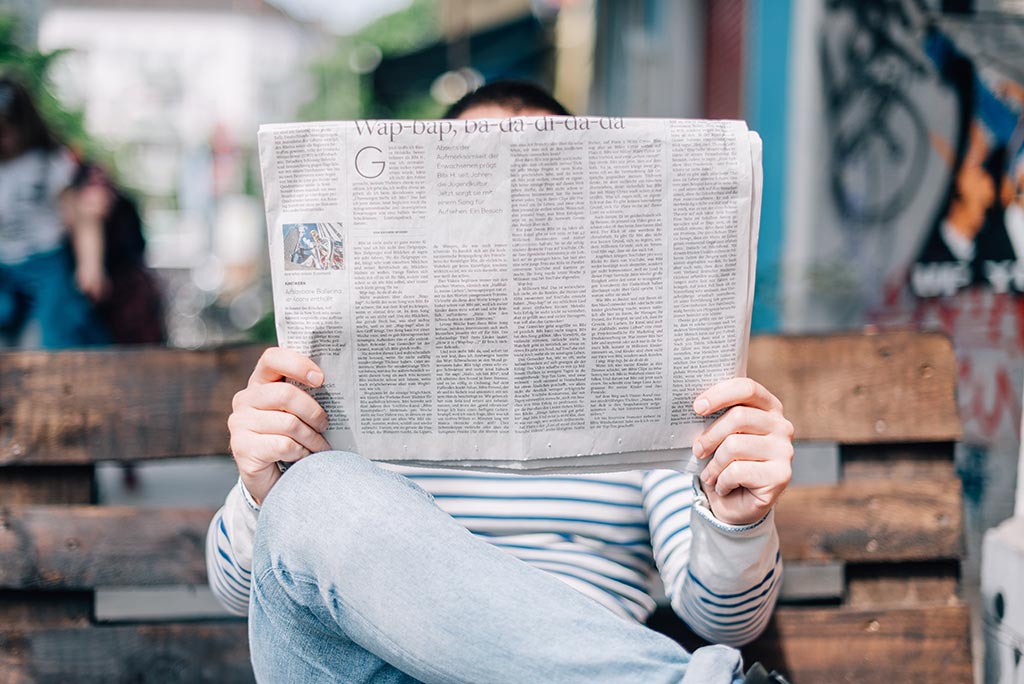
Over the last few years, many entrepreneurs have gained interest in advanced but affordable robots. Also known as collaborative robots, these units are easier to install than conventional robots. They also do not need physical guarding and are easy to move around and program. As a result, cobots can be used in multiple tasks on a daily or weekly basis. To get the best out of synch units, you need the ideal gripper. Here is a guide to help you make an informed choice for your application.Â
Determine the Item you are Gripping
What do you plan to use your robot gripper for? Apart from immediate plans, you also need to prepare for the future. Some of the factors to consider include weight, size, and formation or geometry. Ask yourself the following questions.
- Is the material deformable or solid?
- Will the item change during task execution?
- Can the surface be marked easily?
For instance, if the item is a machined steel object you will need an adequately sized two-finger electric or pneumatic gripper. You could also opt for a self-centering three-finger gripper for a cylindrical object.
For an irregular shaped or soft object then you will need an appropriate end of the arm tool. Suction cups come in handy on slightly curved or flat surfaces, but they could also leave marks on some objects.
An ideal option, in this case, would be a specially designed robot gripper capable of lifting and moving objects with flat or smooth surfaces like food packaging, solar cells, and silicon wafers. Such grippers leverage high-airflow speed to generate a low-pressure area that produces a lifting force for moving work items fast, reliably, and silently. Today, some of the advanced robot grippers in the market can handle pliable, perforated, or porous materials like bubble wrap, metallic mesh, and fabric.
Products whose formation would be challenging for traditional robot grippers can be handled by advanced grippers, which handle customized items regardless of their shape or size. Such gadgets rely on a soft spherical bag with loose particles. Once such a gripper is lowered to the item that requires lifting, the bag filled with particles will have matched up to the surface.
Suction is generated to gather the air from the gaps between the particles. The soft particle bag will then harden and grip the object gently but securely, allowing for its transfer. Once the move is completed, the suction will be removed. The particles will be free to move while the item will be released. Such advanced robot grippers can be used on various items such as bricks, engineering items, and compact fluorescent light bulbs.
Gripping items with a complex formation can be difficult unless they are available in a familiar orientation or position, or the machine vision system can quickly determine their position. When this is the case, gripper jaws matching the surface formation can be developed to facilitate a repeatable, accurate, and safe grip.
The designer will need to work from CAD files to produce the jaw design through computer-aided tools or manually. Recent developments have introduced a web tool capable of developing 3D gripper printed jaws. 3D CAD components are uploaded in STL or STEP format through web-based intelligent software. Users then enter information like the gripper installation position, item weight, and finger length.
The software will create a comprehensive offer with the 3D gripper jaws printing price, delivery time, and 3D contour. 3D printing is ideal for generating complex jaw gripper designs. To handle delicate components that need limited compliance around the gripper, you can leverage any manufacturing processes to produce items in one piece that generates a rigid polymer. The object should have elastomer sections for features that encounter the object getting gripped.
Understand the Operating Environment
Industrial robots can operate in various environments, but different grippers are ideal for different environments. For instance, pneumatics are not ideal when it comes to food processing and packaging.
That is because dirty air may be produced from valve exhaust leaks or valves. In this case, electric grippers would be ideal. However, if a suction cup is ideal where compressed air is not, an innovative gripper with an electric vacuum cup used in multiples or singly fixed on a mounting plate would be ideal.
For dusty ad dirty environments, suction cups can be challenging due to the risk of ingesting particles and fluids that can block airlines and filters. While magnetic grippers may be ideal for handling steel and iron components, improper positioning could trigger problems.
How Demanding the Performance is
Each robotic application is different, meaning that the gripper performance requirements will also vary. For example, high-speed robots for picking and placing tiny objects require a lightweight gripper capable of enduring the loads enforced by high speed. Further, the gripper should launch and close fast to reduce the cycle time.
On the other hand, a six-axis cobot could be executing an easy task. As a result, the gripper weight will be less critical. Quick opening and closing are ideal based on various factors like the workpiece acceleration and deceleration, weight, the gripping force, and the grip type.
The Grip Type Needed
Often, a pair of flat grippers operating on parallel flat surfaces on an object is ideal. However, the grip strength results from the resistance between the object and jaws and the gripping force. It is worth mentioning that the required grip strength is not all about the object weight seeing that robots produce high speeds.
Such accelerations enhance the load applied on the gripper by the object. A robust gripper or a collection of grippers that identify geometric features on a product may be used when a secure grip is required.
If the gripper operates on a cylindrical surface, a gripper with flat jaws and line contact along the opposite parts of the cylinder may be ideal. If the cylinder can be accessed from one end, then a three-jaw gripper could come in handy.
Finally
Robots may be used for various assembly and manufacturing tasks. Remember, you need to choose the appropriate gripper to enjoy automation benefits. Without the right gripper, your task becomes costly to implement and unreliable. Often, the robot performance could be compromised as a result of using a heavy gripper or one that cannot secure items firmly and securely.