Chung-Ang University Researchers Develop Self-Powered Tactile Sensors for Robotics and Wearables
Innovative piezoelectric and triboelectric manufacturing enhances tactile sensors, enabling sensitivity, flexibility, and efficiency for robotics, wearables, and interactive systems.
Image credit: Humanrobo from Wikimedia commons
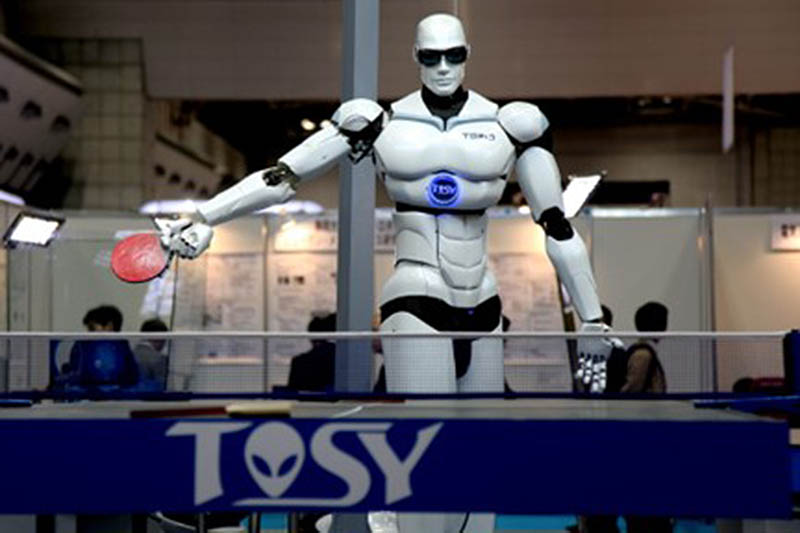
Scientists uncover advanced manufacturing strategies for piezoelectric and triboelectric tactile sensors
Piezoelectric and triboelectric tactile sensors, crucial for applications in robotics and wearable devices, face challenges in flexibility and environmental resilience. In a new study, researchers have developed innovative manufacturing strategies to enhance sensor performance by optimizing material properties and fabrication techniques. These advancements are set to drive the creation of highly sensitive, self-powered sensors for next-generation technologies, enabling breakthroughs in healthcare, robotics, and human-machine interfaces.
Piezoelectric and triboelectric tactile sensors are designed to convert mechanical stimuli into electrical signals, making them critical components in intelligent systems. Piezoelectric sensors leverage voltage generation through mechanical stress in non-centrosymmetric materials, such as quartz and polyvinylidene fluoride (PVDF), while triboelectric sensors operate on contact-induced charge transfer. Both sensor types offer unique advantages, including self-powered functionality and high sensitivity but also face challenges, such as material brittleness and environmental limitations.
A team of researchers led by Professor Hanjun Ryu from Chung-Ang University, South Korea, has introduced novel manufacturing strategies to overcome these limitations. This paper was published on November 11, 2024, in Volume 7 of the International Journal of Extreme Manufacturing. Prof. Ryu explains, “Our study explains the materials and device fabrication strategies for tactile sensors using piezoelectric and triboelectric effects, as well as the types of sensory recognition.”
The team conducted a comprehensive review of manufacturing strategies for piezoelectric and triboelectric tactile sensors, focusing on techniques to enhance sensitivity, flexibility, and self-powering capabilities. The study examined various material properties, fabrication processes, and device designs to overcome challenges, such as brittleness in piezoelectric materials and environmental sensitivity in triboelectric sensors. Prof. Ryu said, “These strategies aimed to enable the development of high-performance sensors for applications in robotics, wearable devices, and healthcare systems.”
For piezoelectric sensors, the researchers highlighted the importance of increasing the piezoelectric constant through methods, such as doping, crystallinity control, and composite material integration. Notable advancements include using lead-free ceramics and polymer blends to create flexible, environmentally friendly sensors suitable for dynamic applications. The integration of 3D printing and solvent-based crystallization techniques was also found to significantly improve the sensitivity and adaptability of these sensors.
The triboelectric sensors were enhanced through surface modification techniques, such as plasma treatments, microstructuring, and dielectric constant optimization. These strategies increased charge transfer efficiency and enabled the development of durable, high-output sensors. The researchers also demonstrated the effectiveness of hybrid materials and nanostructures in boosting triboelectric performance while maintaining flexibility and environmental resilience.
Interestingly, this study is among the first to provide a holistic overview of manufacturing strategies for both piezoelectric and triboelectric tactile sensors, emphasizing their complementary strengths. The findings reveal that a combination of innovative material engineering and advanced fabrication techniques is essential for creating sensors capable of multi-modal sensing and real-time interaction. This interdisciplinary approach promises to expand the application scope of tactile sensors across industries.
The study also underscores the potential for integrating artificial intelligence with tactile sensors for advanced data processing and multi-stimuli detection. Artificial intelligence (AI)-driven analysis of tactile inputs, such as texture and pressure recognition, can significantly enhance the accuracy and functionality of these devices. Such integrations pave the way for next-generation sensors that mimic human sensory capabilities while achieving higher operational efficiency.
Summarizing the broader implications of their work, Prof. Ryu concludes, “It is anticipated that AI-based multi-sensory sensors will make innovative contributions to such advancements in various fields.” This study sets the stage for the development of intelligent systems that seamlessly integrate with human needs, from healthcare monitoring to robotic interfaces.
Reference
Title of original paper: Manufacturing strategies for highly sensitive and self-powered piezoelectric and triboelectric tactile sensors
Journal: International Journal of Extreme Manufacturing
Authors: Hyosik Park1, Gerald Selasie Gbadam1, Simiao Niu2, Hanjun Ryu3,4,*, and Ju-Hyuck Lee1,5
Affiliations:
1Department of Energy Science and Engineering, Daegu Gyeongbuk Institute of Science and Technology (DGIST), Daegu, Republic of Korea
2Department of Biomedical Engineering, Rutgers University, Piscataway, New Jersey, United States of America
3Department of Advanced Materials Engineering, Chung-Ang University, Anseong, Republic of Korea
4Department of Intelligence Energy and Industry, Chung-Ang University, Seoul, Republic of Korea
5Energy Science and Engineering Research Center, Daegu Gyeongbuk Institute of Science and Technology (DGIST), Daegu, Republic of Korea
Corresponding author’s email: hanjunryu@cau.ac.kr and jhlee85@dgist.ac.kr
Funding information: This work was supported by Technology Innovation Program (20025736, Development of MICS SoC and platform for in-vivo implantable electroceutical device) funded by the Ministry of Trade, Industry & Energy (MOTIE, Korea)
About Chung-Ang University
Chung-Ang University is a private comprehensive research university located in Seoul, South Korea. It was started as a kindergarten in 1916 and attained university status in 1953. It is fully accredited by the Ministry of Education in Korea. Chung-Ang University conducts research activities under the slogan of “Justice and Truth.” Its new vision for completing 100 years is “The Global Creative Leader.” Chung-Ang University offers undergraduate, postgraduate, and doctoral programs, which encompass a law school, management program, and medical school; it has 16 undergraduate and graduate schools each. Chung-Ang University’s culture and arts programs are considered the best in Korea.
Website: https://neweng.cau.ac.kr/index.do
About Professor Hanjun Ryu
Hanjun Ryu is an Assistant Professor of the Department of Advanced Materials Engineering at Chung-Ang University. His group is developing nanogenerators for energy solutions, bioresorbable biomedical electronics for wound management, and shape transformable 3D flexible electronics for brain organoid-machine interface. Before coming to Chung-Ang University, he was a Postdoctoral researcher at Jogn Roges’s lab at Northwestern University. In 2019, he received a PhD in Material Science from Sungkyunkwan University under the supervision of Prof. Sang-Woo Kim.
Website:
https://scholarworks.bwise.kr/cau/researcher-profile?ep=1391
https://sites.google.com/view/ryugroup