Explore the Benefits of Predictive Maintenance Programs
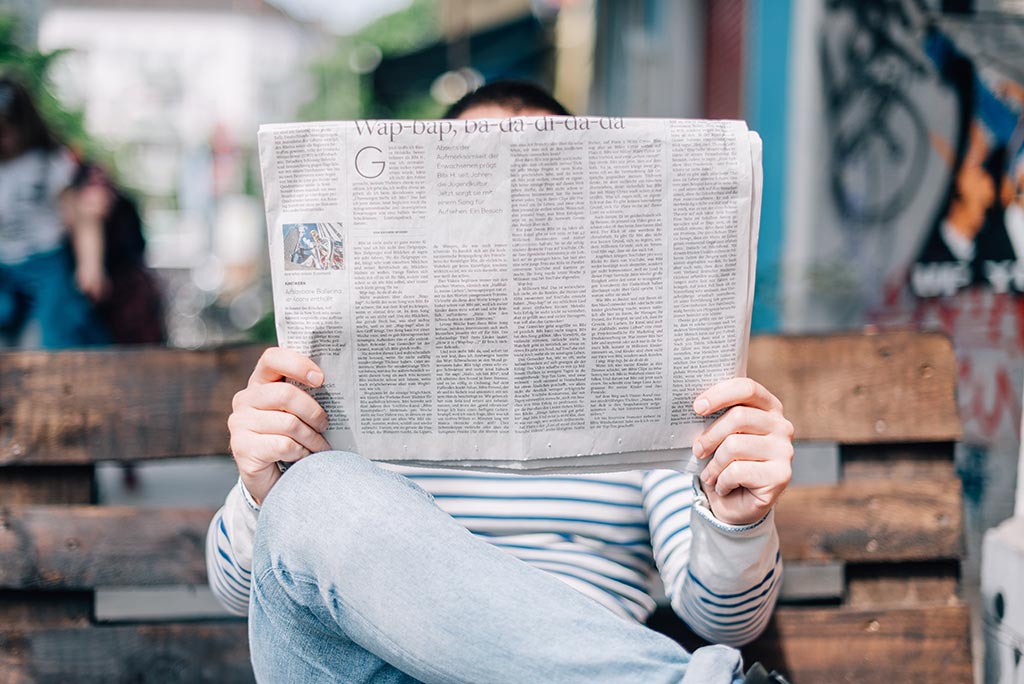
Why PdM Has Now Come to the Fore
By Koyel Ghosh
Well, you can consider predictive maintenance as a corporate philosophy that counts on the state of an organization’s equipment. Monitoring equipment based on the breakdown of data assimilated through on-site inspections, predictive maintenance makes sure any kind of quality issues are taken care of on a prime note.
One of the main intents or goals of predictive maintenance is the authentication of equipment in a timely manner. When it predicts the ensuing problems that may lead to substantial costs, it also paves the way for restorative maintenance. Still, the main aim is to enhance the use of machineries and equipment, thereby creating room for improved productivity and reduced costs for companies.
Though predictive maintenance doesn’t replace conventional maintenance management methods at large, still there’s no doubt that it’s a beneficial as well as relevant practice for building an all-inclusive maintenance management program for an industrial plant. At the same time, when any old traditional program would count on servicing routines for all machineries and a swift response to unpredicted failures, predictive maintenance plans for precise and definite maintenance tasks only when they are really required. And, it might not completely wipe out all facets of old preemptive and counteractive maintenance programs, but it can curtail down the number of unexpected failures, as well as dole out a more consistent scheduling tool for routine precautionary maintenance tasks.
Moreover, when it comes to facilities management, predictive maintenance definitely happens to be an important part of the same. So, in a nutshell, the objective of a successful preventive maintenance program is to show in reliable practices fabricated to perk up the performance as well as safety of the appliances within your business property. Simultaneously, the strategic maintenance of machineries will help enhance equipment life and dodge off any unplanned maintenance bustle. An effective predictive maintenance program is also reliant on the support of all the parties involved. And, the engineering managers on board have got to count on the concepts, notions and knowledge of all the appointed staffs at the property.
But, the fact that the implementation of a preventive maintenance program can be a bit pricey and time taking happens to make room for endless debate as to whether it’s worth fitting in. The question remains, will all the time and capital invest in the plug-in override emergency repairs? According to the experts in this domain, provided, the program is ideally operated, the benefits would definitely outweigh the costs.
The other significant advantages of a properly run preventive maintenance program are as follows-
- Equipment downtime is reduced to a significant extent and the number of frequent repairs is also curtailed down.
- Enhanced management of assets and improved life expectancy of the same, thus eradicating premature replacement of machineries.
- Decreased overtime costs and cost-effective use of maintenance staffs due to working on a programed basis rather than on a crash basis to mend up breakdowns.
- Routine repairs on a timely order evade large-scale repairs.
- Perked up quality conditions for everyone.
So, one would not be wrong saying that predictive maintenance is much likely to make engineers aware of the problems before they happen. And, by directly checking on equipment for troubling signs through these techniques, technicians can effectively detect as well as categorize an imminent machine failure before it ensues and get ahead of the issue before it actually occurs.
Last but not the least; we can profess that the benefits of PdM lie in its capability to radically lessen machine downtime by offering the latest data for assets. By gliding immediate and real-time data into a system right from the machine itself, maintenance experts can perceive if there is any emergent problem and manage them early, before they can wound up to expensive downtime. So, there is no doubt that compared to preventive and reactive maintenance, predictive maintenance program offers the most practical form of maintenance possible.
According to Allied Market Research, the global predictive maintenance market is expected to grow at a significant CAGR from 2019–2026. Increase in demand for transforming maintenance, decrease in operation cost and rising operational efficiency propel the market growth in more than one way. To conclude, we can state that the market is growing quite profusely and in the next few years to come, it’s going to proliferate yet more.
Koyel Ghosh is a blogger with a strong passion and enjoys writing on miscellaneous domains, as she believes it lets her explore a wide variety of niches. She has an innate interest for creativity and enjoys experimenting with different writing styles. A writer who never stops imagining, she has been serving the corporate industry for the last 3 years.