IoT: The Risks Of Relying On Tech
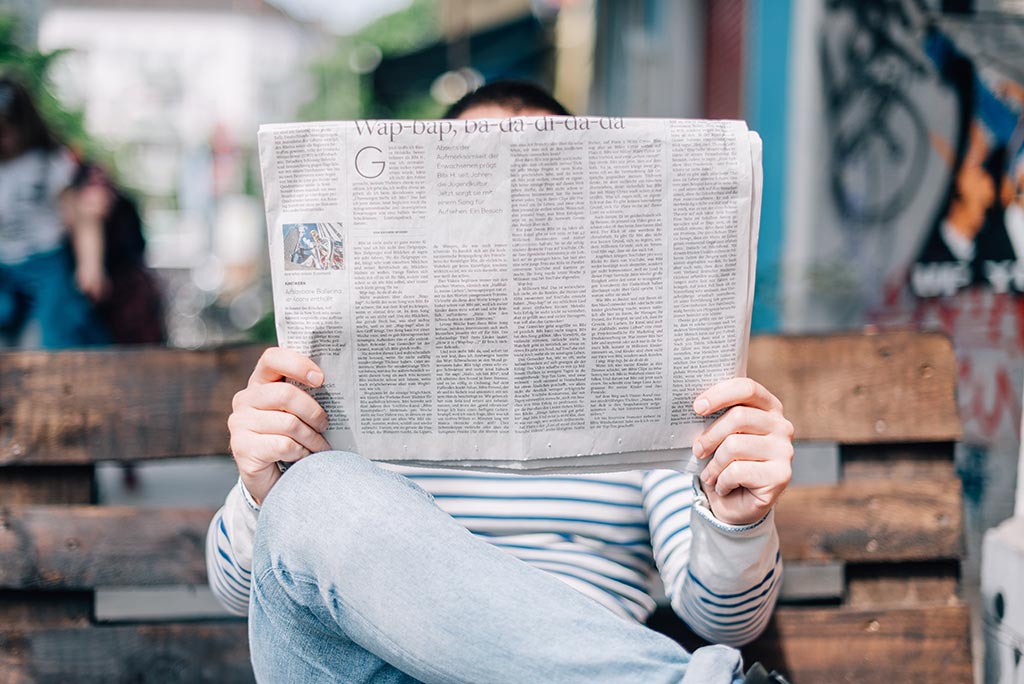
By Roger Brereton
Since its emergence, Internet of Things (IoT) technology has taken the world by storm with its ability to make ordinary objects ‘smart’. The transport industry is no exception. The technology is widely used to enable fleet managers to control and monitor their assets and gain valuable insight into the condition of their vehicles. Roger Brereton of steering system manufacturer, Pailton Engineering, explains why this isn’t enough.

The latest IoT-enabled fleet management systems improve operational efficiency, maintenance costs, fuel consumption and regulatory compliance. In fact, as of 2017, the Federal Motor Carrier Safety Administration in the United States mandated that commercial vehicle carriers and their drivers must use an electronic logging device (ELD) to record a driver’s Record of Duty Status (RODS).
From here on out, approximately three million commercial US trucks now use an ELD connected to the vehicle’s engine and a mobile device, to collect and report useful data.
For condition monitoring, vibration sensors can now be fitted to vehicle steering system parts, to detect negative changes in performance, well ahead of breakdown. Fleet managers are alerted to issues surrounding misalignment, lubrication leakage or corrosion, with insight and projections sent straight to their mobile device.
While this will result in reduced maintenance costs, as repairs are timely, forecasted and local, the use of IoT technology does not get to the crux of the problem.
IoT isn’t adequate
Statistically, some parts may need to be replaced as part of the end-users scheduled maintenance for a fleet, but relentless alerts from IoT networks reflects a much deeper problem that no number of sensors can fix.
IoT technology is only helpful in providing insight into the performance of a vehicle, it will not compensate for poor quality parts. IoT will not make a high-maintenance vehicle part any less high-maintenance. Equally, a low-maintenance part, such as a greased-for-life ball joint, is much less likely to need IoT monitoring in the first place.
While there is certainly room for IoT in commercial vehicle maintenance, adoption of this technology should not be used to mask cheaper or lower-quality parts, as an unscheduled repair or replacement still costs money whether it was detected by a human or detected by a sensor. Additionally, recurrent part replacements will result in much higher vehicle whole-life costs — sensors or no sensors.
This may all sound obvious, but over-hyped technology can often distort perceptions and priorities. Vehicle manufacturers must still prioritise sourcing low-maintenance and high-quality steering parts, from trusted suppliers. Depending on the vehicle specification and application, non-standard features to an individual steering joint or shaft may make all the difference between a high or low maintenance part.
These design elements aren’t often facilitated by some of the mega-multinational steering part suppliers — give Pailton Engineering a call if you need complete design flexibility outside the constraints of a catalogue.
With the right parts installed, commercial vehicle OEMs can benefit from reduced warranty claims or reputational damage, with vehicles performing effectively regardless of IoT technology.
Is it time that everyone stopped talking about IoT? No. For as long as quality and intelligent design is also a priority, IoT will remain a firm part of the sector’s rapid technological development — but we can’t rely on it.
For further information contact:
Roger Brereton
Pailton Engineering Ltd, Phoenix House, Holbrook Lane, Coventry, CV6 4AD
Telephone: +44 (0)2476 680445
www: http://pailton.com/
e-mail: Rbrereton@pailton.com