How To Choose The Right Material for Wire Management Clips
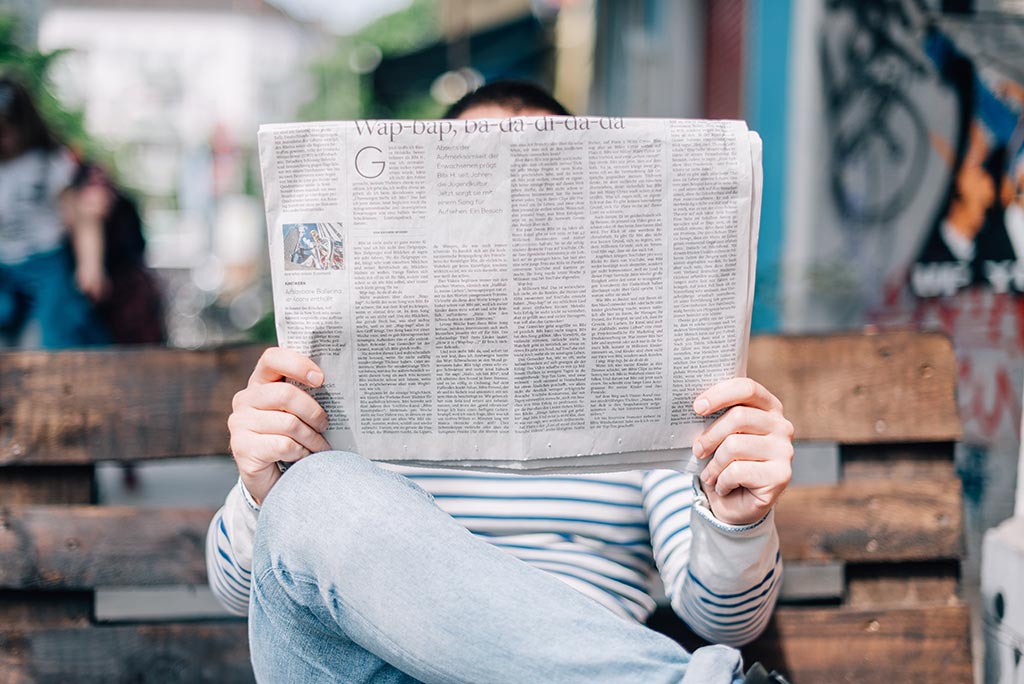
Wire and cable management clips are the unsung heroes of manufacturing, construction, and machine engineering. Can you imagine the mess we’d be without these tiny and cleverly designed components? Luckily, they’re inexpensive and in plentiful supply. There are probably dozens of wire management clips within a few feet of you right now.
When choosing clips for your projects, there are three factors to consider:
- The type of clip
- The material it’s made of
- Its finish or coating
In this article, we’re focusing on the material. Each material has properties that make it suitable for specific applications. To take an obvious example, it would be a mistake—and perhaps a dangerous one—to choose a wire clip with a relatively low melting point for use in a high-temperature environment.
Let’s look at the properties of the three materials most commonly used in wire management clips and accessories.
Acetal
Acetal, also known as polyoxymethylene, is a synthetic polymer used in engineering contexts because it has excellent dimensional stability and impact resistance. It’s frequently used in applications where metal is more common, such as machine parts. In addition to wire clips, you’ll often find acetal used in gear wheels, medical equipment, furniture, and particularly in electrical engineering.
Acetal is an excellent choice for wire management clips because it’s tough, resistant to chemicals, and has a reasonably wide operating temperature range of between -40°F and 180°F. There are different acetal types with slightly different properties, so it’s worth investigating which your wire management clips are made of if you intend to expose them to extreme environments.
Nylon
Like acetal, nylon is a plastic widely used for manufacturing wire clips and fasteners. Nylon is a generic name for a group of plastics manufactured via slightly different chemical processes. Nylon 66 and Nylon 6 are commonly used in manufacturing, and their properties are almost identical, except that Nylon 66 has a higher melting point.
As with acetal, it may be worth investigating precisely which type of nylon you have if you’re putting it in extreme environments.
As a general rule, nylon has many of the same properties as acetal, but it has higher tensile strength and bending stiffness. It can also withstand higher temperatures—although not extremely high temperatures. On the other hand, it’s less well suited for very low-temperature environments.
Nylon is also prone to damage from ultraviolet light, and it does not function well in humid environments—it’s hygroscopic and can absorb water and weaken. Nylon is generally less expensive than acetal, so it’s often used in applications where acetal’s particular strengths aren’t needed.
Steel
Finally, let’s take a brief look at steel wire management clips. Steel is more durable and temperature-resistant than both of the plastics we’ve looked at. It is also stiffer than plastic parts of the same weight. It is, however, typically less resistant to corrosion as well as being heavier and more expensive than plastic parts.
As you can see, wire management clips are available in many different materials. For general applications, acetal and nylon are excellent choices, but you should take care not to use nylon in high humidity or environments where it will be exposed to a lot of ultraviolet light.
About the Author: Adam Price is the Digital Marketing Specialist at G.L. Huyett, a major distributor of nuts, bolts, machine attachments, fasteners, and specialty hardware. They provide high quality materials and manufacturing for a wide variety of industry hardware and specialty parts. For more information, be sure to visit huyett.com or check out their Facebook, Twitter, LinkedIn or Youtube pages.