The Hidden Cost Of Convenience — Why 3D Printing Shouldn’t Be Left Only To An Algorithm
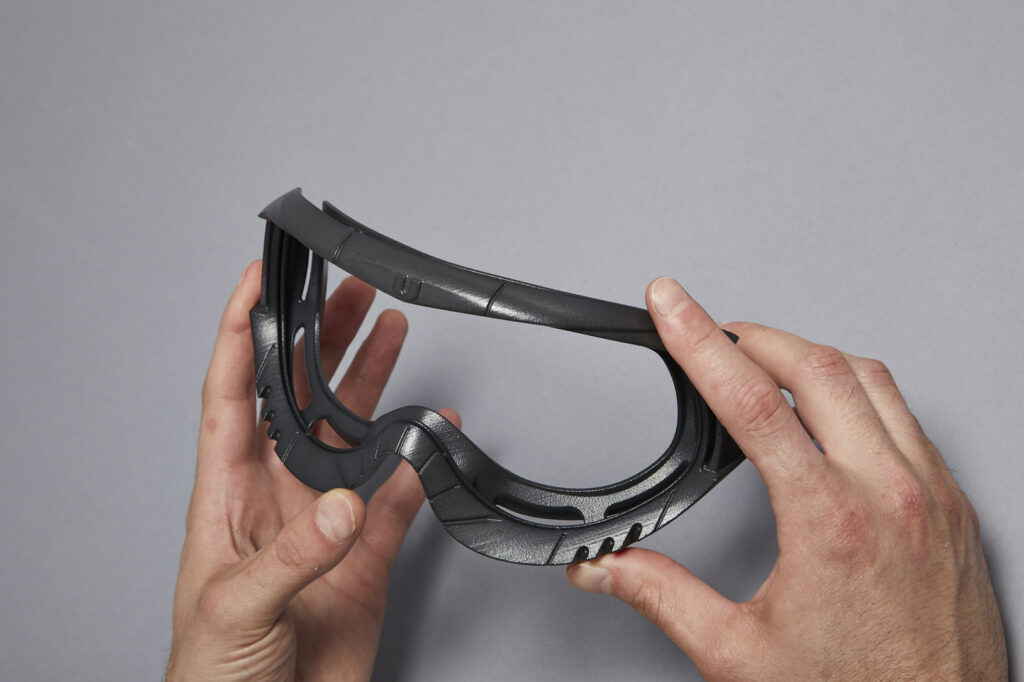
By Sasha Bruml & Felix Manley, Founders, 3D People
In the race to make 3D printing as frictionless as possible, many Additive Manufacturing (AM) bureaus have placed their faith in fully automated quoting systems — sleek, seamless, and designed to get customers from upload to checkout in minutes. It’s a powerful sales pitch. Just upload your file, get an instant price, click a button, and voilà — your parts are in production. No human interaction, no waiting, no hassle.
Sounds perfect, right?
Except, it’s not. Not always. Sometimes the best of both worlds is best.
At first glance, the idea of an entirely self-service 3D printing experience is appealing. Who wouldn’t want an instant quote? Who wouldn’t prefer the simplicity of a few clicks over a back-and-forth exchange with a human? But here’s the uncomfortable truth, when you remove expert consultation from the process, you remove the very thing that ensures the best possible outcome. Automation is great — until it isn’t.
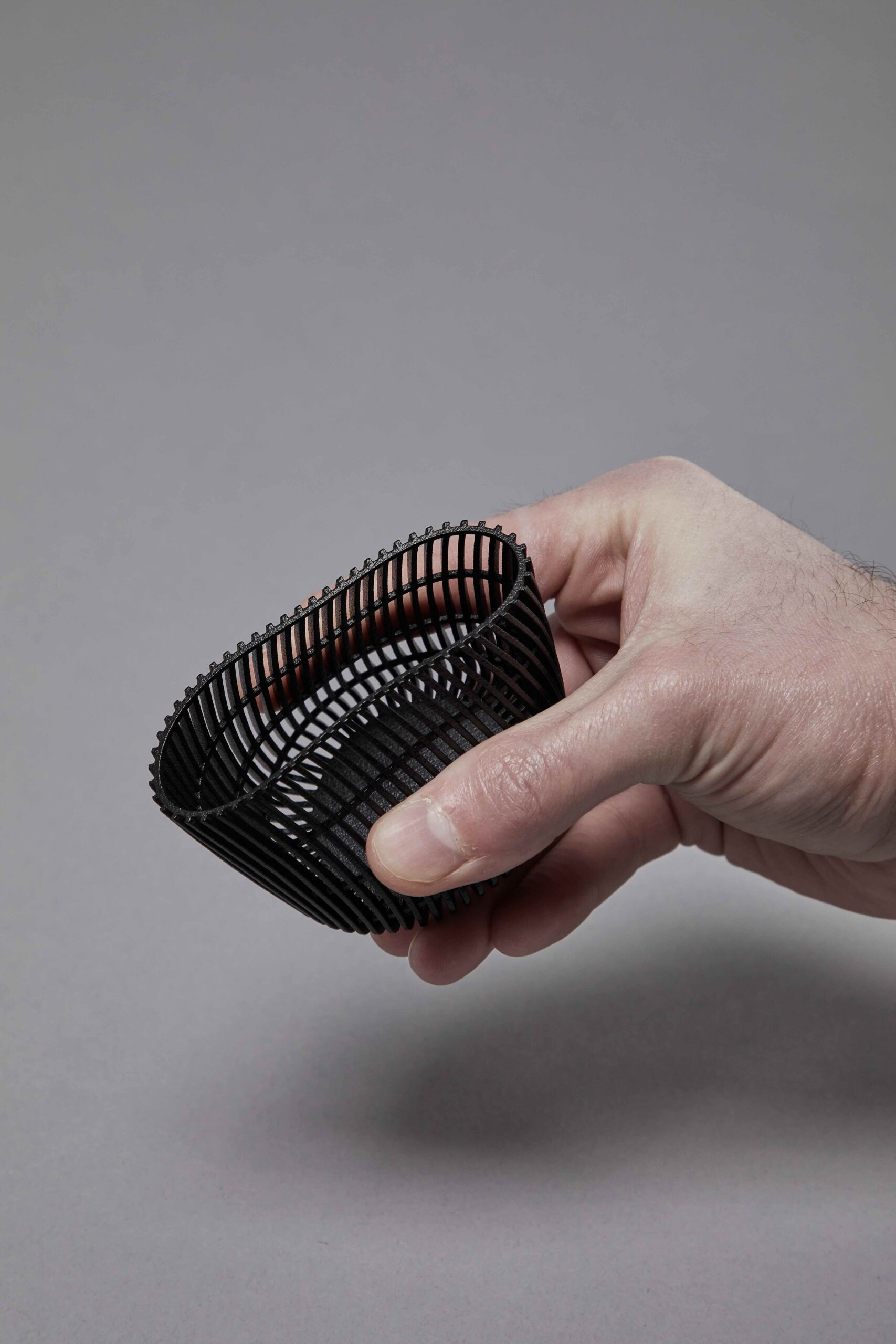
A Quote is Not a Guarantee of Success
Most online quoting systems work on an algorithm. They process your file, assign a price based on material choice and geometry, and generate an estimate. But what they don’t do is think. They don’t fully assess the intricacies of your design, talk to you about your parts application, question whether it’s truly optimised for AM, or flag potential issues before they become expensive problems.
It will accept your file, spit out a number, and let you proceed — right up until the moment when you’ve paid more than you should have for a part that doesn’t perform as expected. At that point, what happens? The system did it’s job to give you a price but it doesn’t care beyond that. Maybe one day in the future it will be able to help optimise your design for cost, ensure you’ve selected the right materials and finishes for your application, or discuss key design features that must function in a particular way – but not today.
Let’s consider a scenario. A product designer uploads a complex part for 3D printing — perhaps a thin-walled component for an industrial application. The system calculates a price, processes the order, and sends it to print.
But what the system doesn’t do is flag that the part design contains features that will likely cause warping. It doesn’t suggest a change that would improve dimensional stability . It doesn’t advise the customer that an alternative finishing process might better meet mechanical stress requirements. So the part prints. It arrives. And it fails.
At this stage, the customer is left with two options. Try again, making modifications at their own expense and without guidance. Contact the bureau, at which point they finally engage with an expert — after losing time, money, and confidence in the process.
This is the reality of over-reliance on automation. It removes the very thing that makes 3D printing bureaus valuable in the first place — expertise.
The Missed Opportunities of Automated Quoting
Even when an automatically quoted part technically prints, that doesn’t mean it’s the best it can be.
Imagine designing a product that’s almost right — but not quite. Maybe the wall thicknesses could be adjusted for a more efficient print. Perhaps a minor tweak in orientation could shave hours off production time, reducing cost without compromising quality. Maybe there’s a better material option, one that would make the part stronger, lighter, or more heat-resistant.
An online system won’t explore these possibilities with you. It doesn’t have the experience of a seasoned additive manufacturing expert, someone who has worked with countless designs, materials, and industries. It won’t push you towards better outcomes — it will just process what you give it, whether it’s the best approach or not.
And that’s the real danger. Not just bad prints. Not just wasted money. But missed potential.
DfAM — More Than Just a Buzzword
Design for Additive Manufacturing (DfAM) isn’t just some industry jargon — it’s the difference between a good part and a great one. It’s what separates those who truly understand 3D printing from those who simply offer it as a service.
DfAM is about optimising geometry for 3D printing. It’s about harnessing the technology’s strengths — lightweighting, complex structures, integrated assemblies — while avoiding its pitfalls. It’s about knowing when a part should be solid and when it can be hollow, where to add material for stiffness/strength, and where it can be removed for lightweighting. .
It’s a conversation. It’s a process. And it doesn’t happen in the seconds between clicking “upload” and seeing a price.
The False Promise of “Faster, Cheaper, Easier”
Automated systems sell convenience, but at what cost? Speed is great — until it means skipping critical steps. Cost savings are appealing — until they come at the expense of print failures and design flaws.
The reality is, 3D printing isn’t always as simple as pressing “go.” Sure, many simple parts can be processed entirely by an automated system and turn out just fine. But when your part needs to do something — when tolerances are tight, materials matter, and failure isn’t an option — you need more than convenience. You need confidence.
That’s why the best 3D printing bureaus don’t only offer online quotes — they offer expertise when required. They combine the efficiency of automation with the human insight that guarantees success.
Because let’s be honest, if your project is mission-critical, if quality actually matters, if performance is non-negotiable, do you really want to leave it entirely to software?
The Hybrid Approach: The Best of Both Worlds
None of this is to say that online quoting tools don’t have value. They do. They’re fantastic for repeat orders, established designs, and rapid price comparisons. When you know exactly what you’re getting, an automated system can save time and streamline procurement.
But they should never replace expert guidance. At 3D People, we believe in a hybrid approach — a seamless online experience backed by real human expertise. Yes, you can get a fast quote. Yes, you can move from file upload to production with minimal hassle. But if you want to discuss materials, tweak a design, optimise for performance or price, we’re here. Because we know that sometimes, a quick chat with an expert can be the difference between a part that works and a part that fails.
That’s what makes the difference. That’s what sets great bureaus apart from those who simply process orders.
The Future of 3D Printing is Personal, for Now…
We live in a world where automation is taking over, where AI is replacing human input at an unprecedented rate. But for the time being, manufacturing is still an industry where expertise matters. And while instant quoting systems will continue to improve, it will be some time before they can contend with the insight, creativity, experience and problem-solving skills of a human who knows what they’re doing.
So next time you upload a file and get an instant quote, ask yourself, is this really the best it can be? Because if you don’t ask the question, you might never know what you’re missing.
Contact 3D People
t. 020 4530 8250
e. print@3dpeople.uk
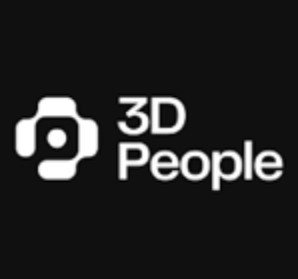
3D People is on a mission to make manufacturing accessible without compromising on quality. Specialising in production-grade parts, 3D People delivers high quality additively manufactured parts using industrial polymer powder bed fusion (PBF) technologies and a range of high-quality finishing options. Prioritising efficiency as a key facilitator, 3D People has developed a proprietary online portal and all parts are made and finished in the company’s London 3D printing facility. From one-off designs through to large repeat production batches, every single part is manufactured to precise standards (ISO 9001) and delivered on time, every time. 3D People’s clients vary across industries including, but not limited to, engineering, automotive, product design, construction, film and energy.