How to Chemically Etch Stainless Steel: A Quick Guide
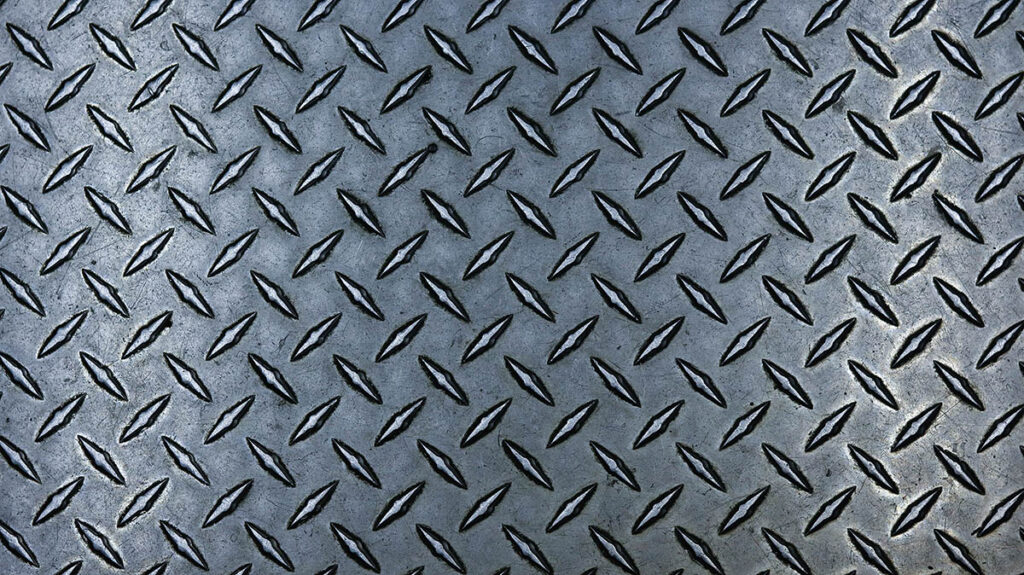
In this article we’re going to take a look at chemically etching stainless steel for the simple reason that it’s one of the most popular choices. This is thanks to its properties, some of which include: high tensile strength, corrosion resistance, durability and temperature resistance. A great many industries such as automotive, medical and communications all use stainless steel within their components for these reasons and more. It’s such a versatile metal that it has a place within a whole host of different applications big and small.
So we’ll take a look at how we at Tecan employ stainless steel and what the actual etching process involves. Just quickly before we take a look at the chemical process, the reason that we use chemicals to etch our metals is because it offers so many benefits, not least being able to have total control over the stencil and final shape of the precision metal part. Other advantages include reduced production times as there’s no need for deburring the metal parts, the metal’s properties are unaffected as it’s not a high energy process like laser or micro-stamping.
The Manufacturing Process
It is essentially a subtractive production process whereby a carefully formulated chemical etchant is applied across a sheet of metal. The etchant then dissolves the unwanted parts of the metal and what we’re left with are the complex and precise metal parts! This is the outline but now let’s take a look at the manufacturing technique in a bit more detail:

1: Clean
Of course the first step is to thoroughly clean the sheet metal so that it’s rid of any surface contaminants which will ensure the future success of the chemical etching process.
2: Laminate

The lamination process happens in a class 6 clean environment (an enclosed room with HEPA filters and more) to ensure that the photoresist lacquer is applied correctly. The laminate is to preserve the parts of the metal we wish to keep while the rest is dissolved.
3: Expose

Here the sheet metal is ready to pass through UV lamps whose purpose is to harden the photoresist into its desired pattern. In the image, the white areas represent this hardened photoresist while the black are the parts that will be dissolved by the etchant.

4: Develop
Here the un-exposed photoresist is developed away to leave the bare metal underneath. At this point the sheet metal is ready for the chemical etchant.

5: Spray
Here is where the chemical etching process really takes place; we spray the entire sheet metal from a number of nozzles to cover it evenly. Then the dissolving process begins and acts across the entire sheet metal.
6: Strip

In this final stage the etchant has removed the unwanted parts and the photoresist is finally stripped as it’s no longer needed. Because it’s a chemical process there are no burrs or stresses on the metal which makes chemical etching incredibly efficient and, as a result, quick as well.
Where is Chemical Etching Used?
As you can see there’s the potential for a great number of applications thanks to chemical etching’s ability to produce precise metal parts without compromising the material’s inherent properties. Today we are seeing chemically-etched parts in an increasing number of products including speaker grilles, bipolar fuel cell plates, mesh filters, stencil and squeegee blades and many more. Thanks to its incredibly efficient process, this manufacturing technique can be scaled up to an industrial level if the total quantity is required.
As mentioned previously, the process doesn’t require any secondary production which means that it’s perfect for electronic mating components that require absolutely exact measurements and shapes as well as metals with high conductivity. It’s the same for manufacturing bipolar fuel cell plates that specifically need non-directional channels etched into the surface. By using chemical etching, it’s easy to create the precisely measured fluidic channels that are required in bipolar fuel cells.
The Advantages of Using Chemical Etching
I’ve mentioned a number of the advantages so far but what they really boil down to are efficiency, speed and complexity of design. We know how efficient the process is as, by using a chemical process it means there’s no post-production necessary to finish the product before it’s used within its required application. This also translates to quick lead times as the initial prototyping is a smooth process that only requires amends on computer software until the final design choice is settled upon. The total production times are quick too as the chemical process gets to work across the entire sheet metal so that everything takes place concurrently – it’s only a matter of cleaning the metal at the end to make sure it’s free of any residues.
The complexity of design is also a great advantage as it’s only limited by what is possible to create on computer-assisted design software and the physical metal that’s being worked on. This means that intricately-shaped parts can be constructed without any challenge, because it’s a chemical process it would be just the same as etching out a simple square for instance.